AI-Fire: Advanced AI Technology for Fire Ignition Video Analysis
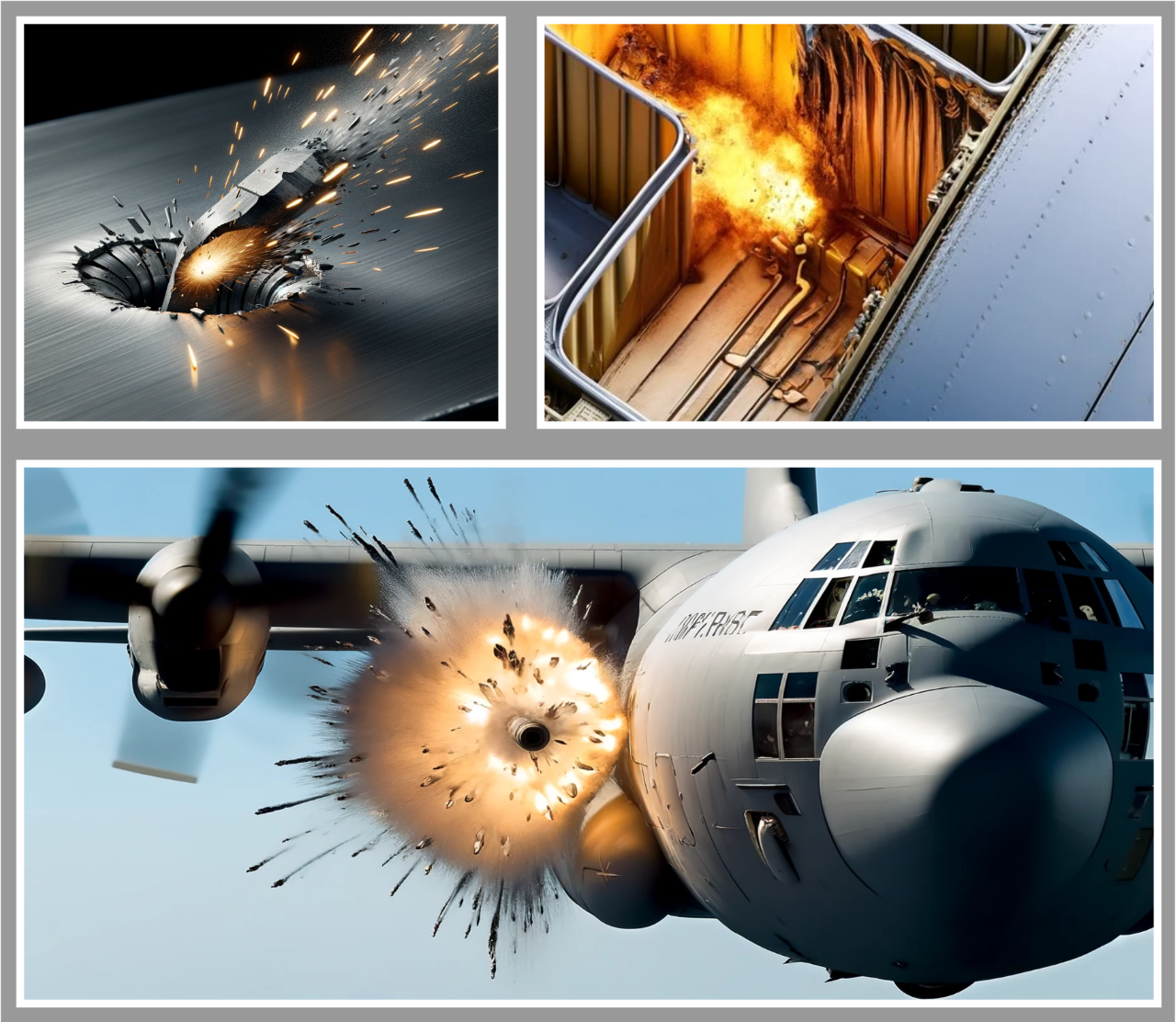
Fire ignition analysis is often used for aircraft survivability, munition effects analysis, and operational safety improvements. However, analyzing fire ignition events for these purposes poses unique and complex challenges. Traditional tools, such as Wildfire Ignition Analysis, FireWatch, and NASA FIRMS, are not tailored for the high-intensity, collision-induced ignition scenarios typical in military contexts. Filling up this gap, AI-Fire is an advanced, AI-powered software tool specifically developed for real-time detection and analysis of fire ignition events resulting from high-impact collisions. It captures the full fire lifecycle, from inception and growth to peak intensity and decay. Unlike conventional approaches, AI-Fire excels at modeling the intricate interactions among penetrating fragments, incendiary agents, and system damage, which often complicate and delay accurate assessments. More specifically, AI‐fire is able to quantify the explosive impacts by collectively measuring the flash time, orientation, spreading, and other metrics, including:
- Projectile Impact Orientation: Roll, Yaw, and Pitch and their evolution over time,
- Flash Angles: Top Yaw (FFF and BFF), Side Pitch (FFF and BFF), and
- Flash Extents: Top and Side under different Obliquity Setups.
For example, AI-Fire can be leveraged for Air Force Test Center to enhance their fire testing protocols for aerospace vehicle survivability analysis. A set of analytic metrics are provided for Air Force to develop preventative measures for improving aerospace & vehicle safety. Further, the analytic result could be used to develop fine-tuned ignition processes to improve ammunition accuracy, range, and effectiveness to develop new advanced ammunition. In addition to DoD usages, AI-Fire improves the survivability and safety of commercial vehicles, aircraft, buildings, and public infrastructure. For instance, AI-Fire can be used for Commercial Aircraft Fire and Impact Testing. It can also be used National Highway Traffic Safety Administration (NHTSA) uses high-energy impact tests and post-crash fire testing to assess. Potential customers could be Tesla, Bolt, and other EV manufactures for battery fire risk test & analysis. Additionally, it can used for DHS and FEMA LFT&E-type testing analysis for Explosive containment rooms, Protective doors, windows, wall sections, Simulation of Vehicle-Borne Improvised Explosive Device (VBIED) effects.